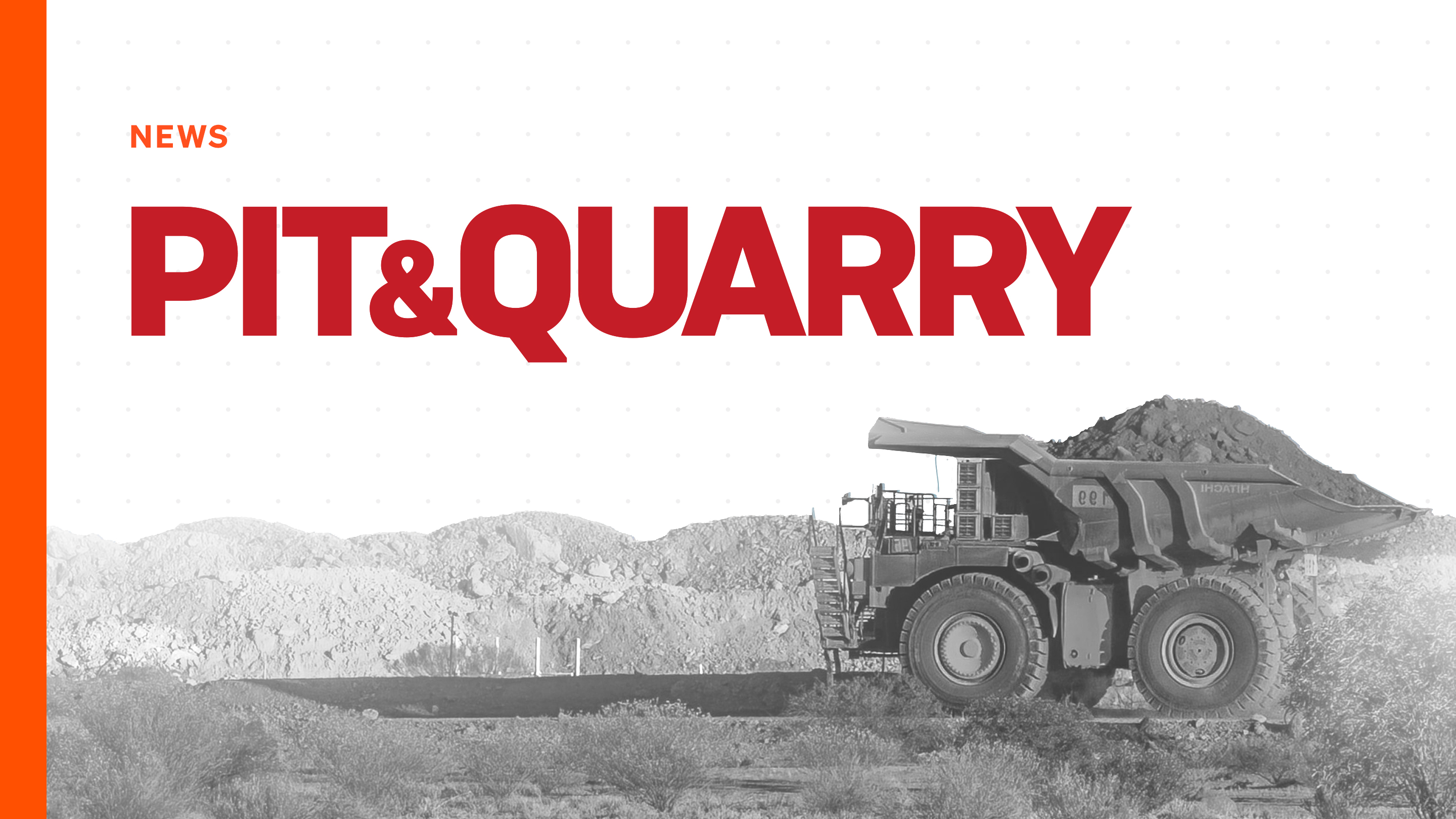
What’s next with Autonomy?
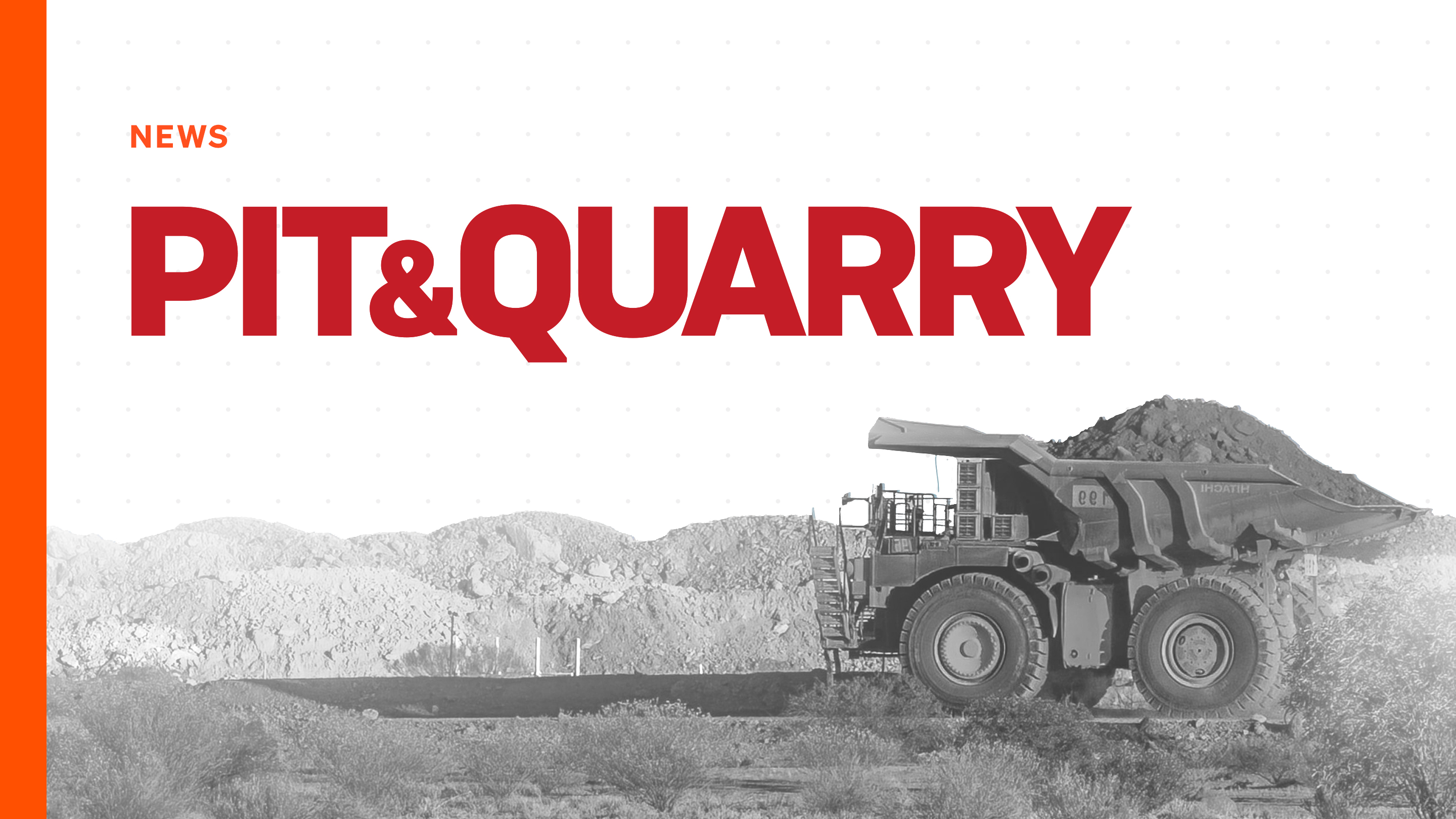
Some of the largest aggregate producers in the nation are currently exploring the feasibility of autonomous technology within their haul truck fleets. Among these is CRH, which is exploring the feasibility of autonomous tech through a program with SafeAI.
To learn more about the CRH-SafeAI partnership but also the broader road ahead for autonomous tech within aggregates, P&Q’s Kevin Yanik caught up with SafeAI founder and CEO Bibhrajit Halder
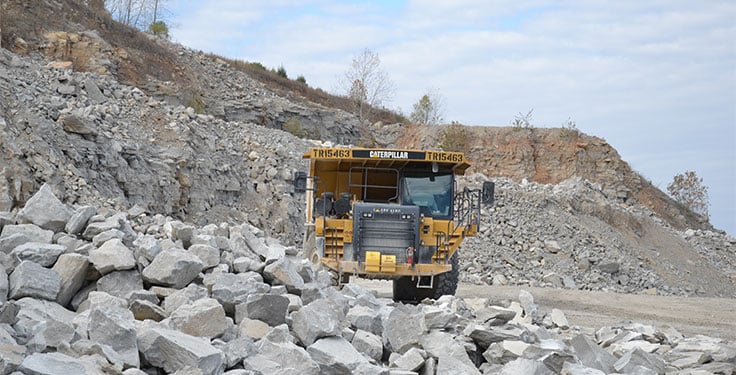
Autonomy is obviously present in mining and it’s clearly coming along in aggregates, but why are we now seeing projects take off? Also, who’s driving these projects? Is it the technology providers or the aggregate producers?
HALDER: The question ‘why now’ is a loaded question, but it’s a very timely one.
It’s not just autonomy right now. Autonomy is obviously there. Digitalization is also very interesting, and electrification is a major focus of this industry. Right after we made the announcement to partner with CRH to do autonomy, notice how Caterpillar and CRH came out with an announcement to focus on electrification.
My point is that producers are looking at autonomy, digitalization and electrification at the same time. And it’s not just CRH, but it’s the CRHs of the world that are actually driving this. They’re not just talking to us, but they’re talking to Caterpillar and other service and technology providers.
They are thinking about their next 10 or 15 years and what the future of aggregates looks like. These are the three critical pieces, and ‘why now’ really comes down to the dollar. The technology has been there for autonomy in mining, but it was way too expensive for [aggregates] to even look at.
Let me give you a datapoint: The mining industry implemented autonomy 10 years ago, and they paid about $10 million just to set up a network. This does not even include trucks; this was exclusively to set up a network.
If you think about companies like BHP or Rio Tinto, they’re running a mine for 20, 30 or 40 years. They’re making billions of dollars of operating income on that. For them, a $10 million cost to set up a network in one mine makes sense. They can amortize the cost. But an aggregate producer cannot possibly put $10 million into a project like that.
Now, however, that $10 million cost is down to $300,000. All of a sudden, a discussion can be had.
A second thing that’s happened is the technology has matured. The first version of this was not ready for aggregates. This application involves a lot more variability and complexity than mining.
Also, mining pays about $200,000 to $300,000 per year per truck for this technology. An aggregate producer cannot afford to pay this. They want to pay somewhere from $60,000 to $100,000 per year per truck, but their application is complicated.
So why now? The maturity of the technology has improved, and the cost went down.
One more thing I’ll say: Companies like CRH and others are not just looking at this as a pilot. They have a long roadmap and a desire to replicate and scale up into hundreds of aggregate operations around the world.
What’s ‘the floor’ on who can get into this space within aggregates? Do you need to have a certain size fleet or so many operations for this to be scalable? Also, what’s the nature of the aggregate-producing company that can get involved in autonomy?
HALDER: The large producers will lead – and we’re already seeing them lead this. It will probably spill over to upper-tier medium producers, but the smaller ones probably cannot get it today. There is a preparation that goes into making an operation autonomous, and projects can take about a year at minimum.
A second thing is the equipment: It must be no more than 10 to 12 years old. If it is too old, producers don’t want to put extra money on that vehicle for it to only run for two more years before it’s done.
Also, it’s ideal to look at equipment that is run in the same application repeatedly, hour after hour. Some of the smaller-size equipment is involved in a lot of tasks. So, you’re looking at vehicles that are longer operation in nature and doing repetitive things. This includes mainly trucks, dozers, excavators and rollers.
We very much talk about trucks when it comes to autonomy. You’re saying dozers, excavators and rollers have similar potential?
HALDER: We actually made a dozer autonomous last year. Eventually, we will also go after an excavator or a loader.
Why is the haul truck the first piece of equipment producers and technology companies are targeting? Also, compared to haulers, how much more dynamic is the environment around dozers, excavators and rollers?
HALDER: A haul truck is the easiest from the technology point of view. Haul trucks are also a good indicator of how an operation is doing. The more haul trucks are moving, the smoother the operation is running.
They also do a very repetitive thing. They’re doing the same work again and again. There’s no variability.
Also, the truck driver only drives the truck. The excavator operator does a lot more than excavating. If you look at their salary grade, the truck driver makes the least and the excavator operator makes the most. The excavator operator is actually a senior person who not only does the digging, but that guy comes out of the machine and manages the whole beat of the operation.
How far behind are we in making some tangible gains on these other equipment areas we’re talking about?
HALDER: Let me give you our ‘bottom up’: We just kickstarted a project. Our goal is that the truck should give 20 percent more productivity than a human-operated truck. We’ll first try to hit 100 percent, and then we’ll aim for 120 percent. That’s our goal, and that’s what the industry is demanding. Once we nail that truck down, then we’ll utilize that knowledge and propagate it to other equipment.
We see companies like CRH and Luck Stone announcing their involvement in autonomy. Where are the industry’s other large producers right now when it comes to this technology?
HALDER: The interest is massive. Everybody is interested, but not everybody is jumping to talk about it because this is a heavy technology. It’s not a quick-to-integrate technology. They want to be careful.
We also want to be careful, because if you deploy this technology and it doesn’t work out, that’s going to backfire the whole industry. We don’t mind actually being slow.
We’ve talked to seven or eight of the bigger producers in aggregates, and they are all very interested. We are extremely excited about the work we are doing with CRH. As we deliver, the whole industry is going to watch. If we can deliver positively, you’ll see almost a domino effect. But we also want to make sure we do it right.